Apmp Pulping Technology And Its Development Potential In The World Market
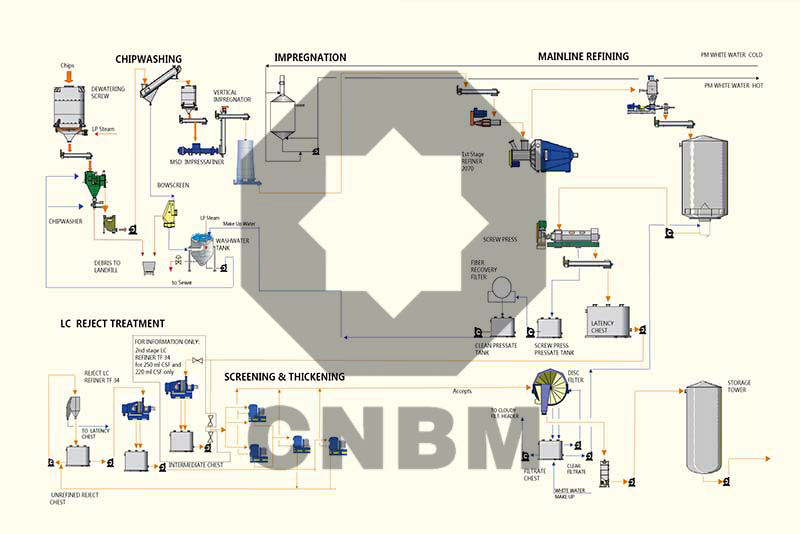
APMP pulping process
On the basis of BCTMP, the APMP pulping process was developed in 1989 by ASB company, namely Alkaline Peroxide Mechanical Pulp. It has the outstanding advantages of super high yield, good pulp strength, less pollution and low energy consumption. It breaks the traditional concept of pulping and finishes cooking and bleaching simultaneously in a single chemical pretreatment process, which greatly simplifies the pulping process. Reduce investment costs by 25% or more. APMP pulping is a typical two-stage alkaline hydrogen peroxide pulping process, which is mainly divided into wood washing, pre-steaming, squeezing, impregnation, pulp grinding, screening and so on.
Water flake washing
The wood chips from the self-contained material system enter the wood warehouse. In order to obtain better washing effect, the wood chips were heated to 60 ℃-70 ℃ in the warehouse and stayed for 20 min. After washing, the pieces are sent to an oblique dehydration screw, and then into the first stage of steam storage. Pieces of wood are stirred in the scrubber to remove surface debris, such as sand, stones, metals and other debris, which are deposited at the bottom of the chip scrubber and can be removed periodically. Washed pieces of wood are pumped to the dehydrated screw. A perforated sieve plate on the dehydration spiral that opens the wood and moisture. The water produced by the chip washing system separates sawdust and other debris through a skew screen.
The scum in the washing water can be precipitated and discharged regularly. Washing water after washing wood chips, a part of which is used as supplementary water for the chip scrubber. The rest was sent to the sewage treatment plant.
Two-stage impregnation
-
First stage impregnation
After washing , the wood chips enter the normal pressure pre - steaming chamber ( about 95℃ for 5-8min ) , pre-steamed at atmospheric pressure to remove air of the wood chips , soften the wood chips to facilitate the mechanical compression and impregnation of the wood chips. The steaming pieces are then fed into the screw tearing machine MSD with a compression ratio of ≥ 4: 1. The dry degree of wood chips can reach about 60% after pressing. Squeezing can squeeze the air in the wood, excess moisture and resin, etc., and crush the wood into pieces of wood. In this way, the solution and fine impurities are removed, and the impregnation effect of the chemical solution is improved.
Loose wood silk groups can contact as much as possible with the solution and easy to permeate the chemical solution. The main chemicals used in impregnation are NaOH H 2O 2 and peroxide stabilizers such as DT-PA or EDTA, sodium silicate, magnesium salt. The addition of NaOH softened fiber (mainly to soften the heterogeneous parts of hemicellulose and cellulose) can improve the strength of the paper pulp and reduce the content of chips. Reduce energy consumption of grinding pulp. Adding H2O2 can improve whiteness and soften lignin. After a period of time (about 2 minutes) in the impregnator, the wood slice is raised to the upper part of the impregnator by the preimpregnating spiral to remove the excess liquid, and sent to the first reaction chamber (70 ℃-75 ℃) through the normal pressure spiral. Stay for 25 min so that the impregnated wood can fully interact with the chemical solution. -
Second stage impregnation
Out of the first stage of the reaction chamber, the wire mass is often pressed to transport the screw to the second stage screw tearing machine. The extruded fibers were fed into the second stage impregnator, and then the impregnated fibers were sent to the second stage reaction chamber (stay 4O-45min, temperature 70-75℃, equivalent to H2O2 bleach), and the reacted fibers were fed into the first disc mill by metering screw. The main purpose of the second stage impregnator is to improve the whiteness of the paper pulp by using alkaline H2O2 solution with low alkalinity H2O2 content.
Two-stage disc grinding pulp
After grinding, the paper pulp stays in the tank for a period of time, and the paper pulp concentration is 4%. Generally, APMP is a kind of atmospheric pulp, and the pressure of grinding area is lower, so as to reduce the invalid decomposition of H2O2 and improve the whiteness of the paper pulp. A large amount of white water is added to the diffuser to condensate the steam in the paper pulp and dilute the paper pulp up to 35-45%. After storage in the intermediate paper pulp tank for a period of time, the pulp was pumped to the screw tearing machine for washing and concentrated to a higher concentration, and then the two-roller metering screw was used to enter the second stage of the grinding pulp with a normal pressure disc. After grinding, the paper pulp stays in the tank for a period of time, and the paper pulp concentration is 4. After dewatering and squeezing out the filtrate from the spiral, sieving the fibers contained in it, the filtrate enters the pool tank for intermediate washing and dilute use.
A sewn screen
In order to remove fiber bundles, sifting sieve with 15mm width is selected to select the paper pulp. The good pulp is sent to the low consistency pulp tank with 10% to 15% concentration, then concentrated to 12% by disc concentrator and sent to the high consistency pulp storage tower, and diluted to 35% concentration at its bottom to the papermaking workshop.
APMP paper pulp properties
The chemical and energy consumption were lower than BCTMP, while the brightness, strength and opacity of pulp were higher than BCTMP. The product of APMP pulping system is equal to or superior to that of hardwood. The combination of APMP pulping and bleaching process reduces the cost of construction. A simple atmospheric disc mill can be used, without the need for a large steam system, the discharge of waste water load is low, no sulfur compounds. The energy consumption of APMP is low under the same degree of dissociation. The tear index and tear index of APMP were higher than that of BCTMP. The whiteness of H2O2 was high when the dosage was the same. The chemical and energy consumption were lower than BCTMP, while the brightness, strength and opacity of pulp were higher than BCTMP.
The comparative analysis of poplar test shows that the outlet of the second stage disc mill can be completely bleached in the process of APMP production, and its strength properties can be fully played, no further bleaching workshop is needed, and the energy consumption is the lowest. The comparison and analysis of eucalyptus showed that the APMP paper pulp was prepared by two-stage impregnation with alkaline hydrogen peroxide, and compared with the one-stage impregnation process and the BCTMP process, according to the data provided by Hymac Company of Canada. The APMP with two stages of impregnation can increase the yield of BCTMP by 55%, and the power consumption is 25% lower than that of BCTMP, and the opacity is 5% higher than that of CTMP. So it is more economical to adopt APMP.
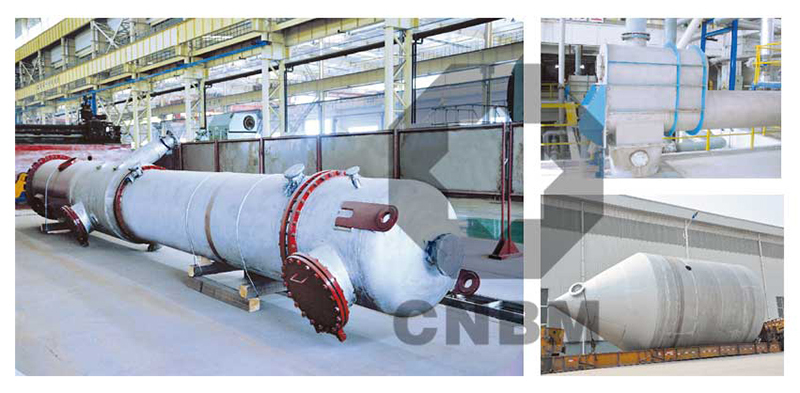
The present situation of Development in the World Market
As a new energy-saving and environment-friendly pulping technology, APMP has the outstanding advantages of high yield, high brightness, high intensity and low pollution, low water consumption, low energy consumption and low material consumption, and is regarded as the best pulping technology in the present century. Has been the world pulp and paper industry attention. Once developed, many developed countries began to adopt the pulping technology, and one after another emulated the development. At present, the study of wood fiber pulping abroad has been successful in the application of wood, spruce, pine and other pulping materials to newsprint and culture paper. The study of non-woody fibers is still in its infancy.
APMP has been widely used in developed countries as its main pulping technology and pulping equipment. And the research on the wider applicability of the technology has never stopped. The majority of developing countries have also begun to introduce and apply this advanced technology and equipment to pulping. The development potential of APMP in the world market is huge.
CNBM is one of the leading paper pulp machine manufacturers in the field of paper pulp machinery. Our company's leading products include large chemical containers, tower, reactor, heat exchanger, complete pulping production line, intermittent cooking equipment, large-scale chemical pulp production line, complete set of pulping equipment APMP paper pulping process, multi-disc vacuum filter and other complete sets of paper pulp machines. Welcome friends from all over the world to contact us!
Leave messages for quotations and solutions. The average response time is up to 24 hours. Your privacy is protected. Check privacy policy here.